Sheet Metal Fabrication
Competitive Prices
Affordable and precise laser-cut profiles at competitive rates.
Fast Turnaround
Quick and reliable laser cutting with fast turnaround times.
Nationwide Delivery
UK Delivery: Reliable laser-cut profiles shipped nationwide.
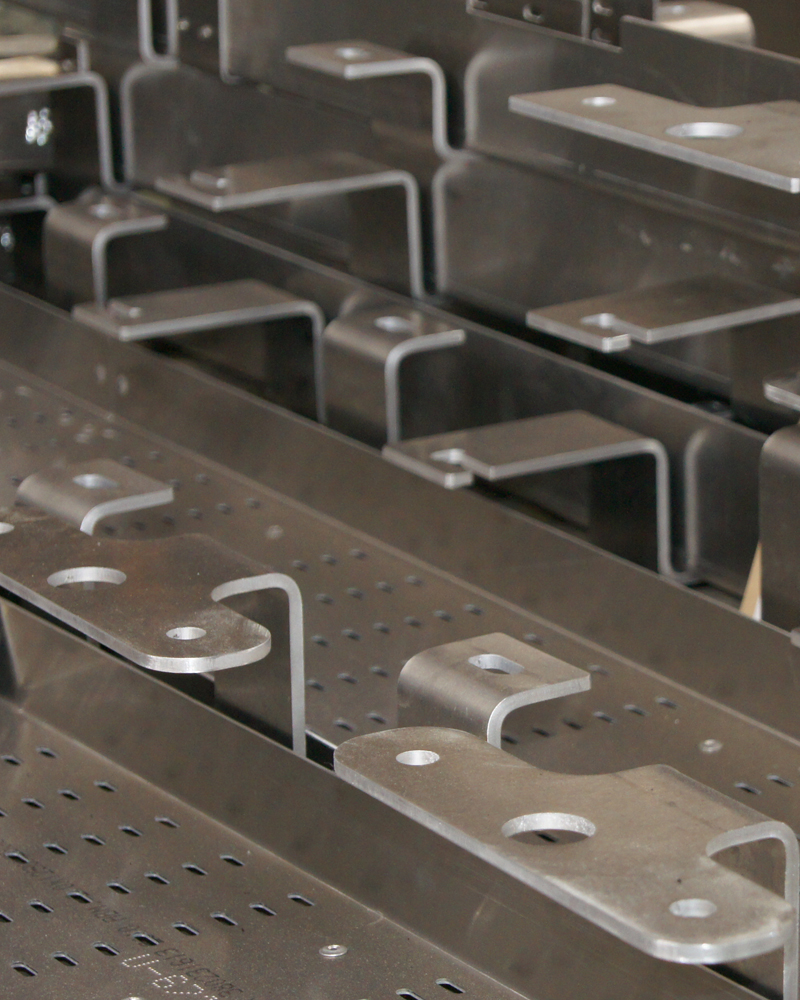
Sheet Metal Fabrication Services
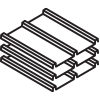
Press Braking
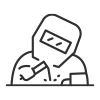
Welding/Fabrication
Sheet Metal Fabrication Services
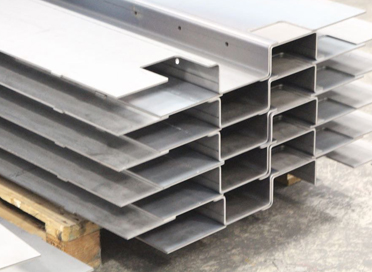
Press Braking
Press braking is a metal forming process that bends sheets into precise shapes using a press brake machine, essential for manufacturing accurate components.
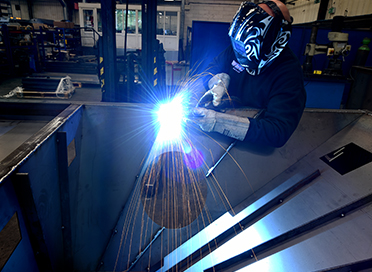
Welding & Fabrication
Welding is a fabrication process that joins materials, usually metals, by melting and fusing them, essential for creating strong, permanent bonds in manufacturing.
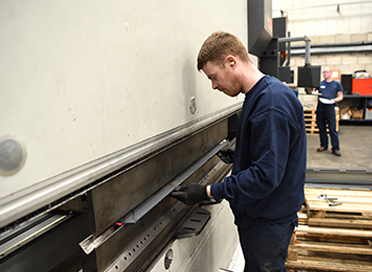
Folding/Bending
Fabrication is the process of cutting, shaping, and assembling materials, typically metals, to create structures and components, essential for manufacturing a wide range of products.
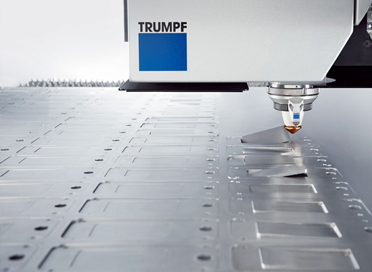
Sheet Metal Laser Cutting
Sheet metal laser cutting is a precise process that uses a laser to cut metal sheets into specific shapes and sizes, essential for detailed and accurate manufacturing.
Laser Profiles use ISO 9001:2015 to drive production, ensure full traceability and satisfy customer needs
Laser Profiles strives to provide exceptional engineering and fabrication services. Quality is integral to our operations, as shown by our accreditation to the most recent standards and our dedicated in-house QA team that carefully inspects each part. Our chief aim is to exceed our customers’ needs and expectations.
Drawing on extensive experience, we serve a broad customer base in industries including aerospace, defense, nuclear, marine, and oil & gas.
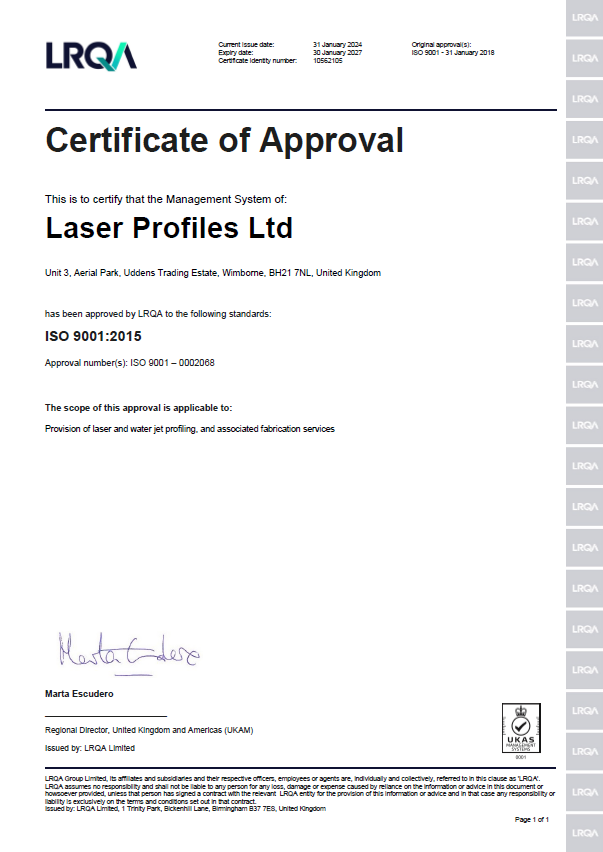
Frequently Asked Questions
Sheet metal fabrication is a manufacturing process that involves the creation of structures and components from thin metal sheets. This process includes various techniques such as cutting, bending, punching, stamping, welding, and assembling.
Cutting involves dividing the sheet metal into smaller pieces using tools like shears, laser cutters, plasma cutters, or waterjet cutters. Bending shapes the metal into specific angles or forms using press brakes, rollers, or folding machines. Punching creates holes or indentations in the metal, while stamping imprints designs or shapes onto the surface.
Welding joins pieces of metal together by melting and fusing them. Assembling combines various fabricated metal components into a final product through methods like riveting, fastening, or welding. Finishing processes, such as polishing, painting, powder coating, or anodising, enhance the surface of the metal product. Sheet metal fabrication is used across numerous industries, including automotive, aerospace, construction, electronics, and consumer goods, to create parts and structures ranging from small components to large assemblies.
Sheet metal fabrication offers numerous advantages that make it a preferred method for producing a wide range of components and structures.
One key benefit is its versatility, as it can accommodate various metal types and produce both simple and complex shapes with ease. This flexibility allows for the creation of custom designs and adaptations to meet specific requirements.
Additionally, sheet metal fabrication is often cost-effective, particularly for large-scale production, due to the efficiency of modern techniques like laser cutting and stamping, which reduce the cost per unit.
The strength and durability of sheet metal components are another significant advantage, as metals used in fabrication are known for their robustness and long-lasting properties. Precision and accuracy are also noteworthy benefits, thanks to advanced fabrication methods such as CNC machining and laser cutting, which ensure that parts are made to exact specifications. This precision reduces the likelihood of errors and improves the overall quality of the finished product.
Efficiency in production is enhanced by the speed and automation of fabrication processes, which help in reducing lead times and increasing output. Moreover, many metals used in sheet metal fabrication are recyclable, supporting sustainable manufacturing practices and minimising waste. Finally, sheet metal can be finished in various ways, such as painting or powder coating, allowing for both functional and aesthetic enhancements to meet different design needs.